
Contact us
Inventory Management
Efficient Shipment Inspection and Receiving: Best Practices
Feb 3, 2025
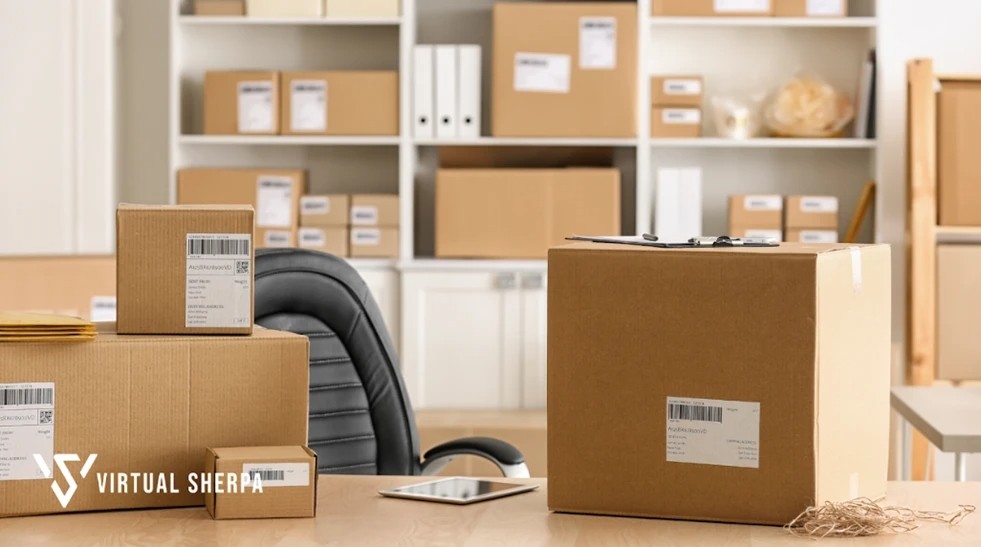
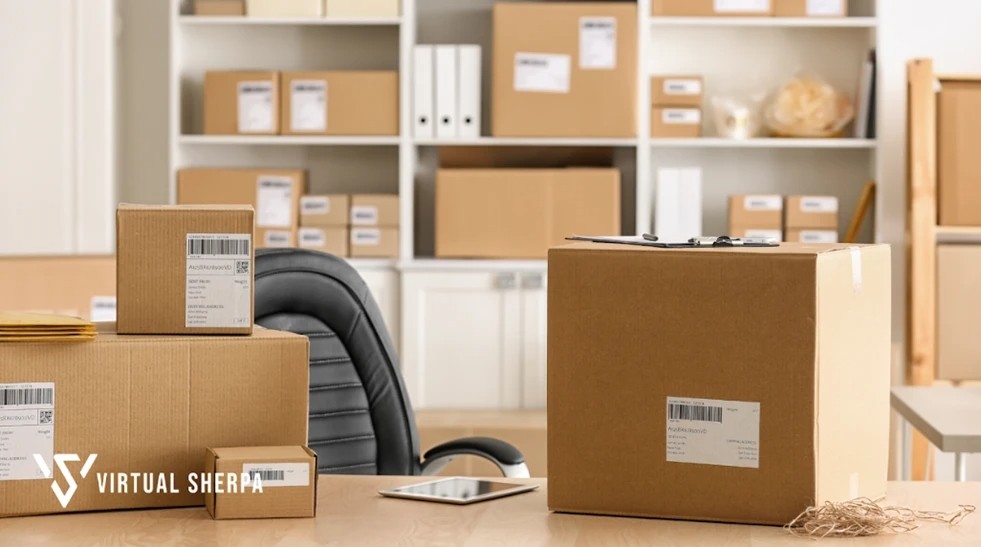
In the fast-paced world of inventory management, ensuring the accuracy and quality of incoming shipments is crucial. Every missed step or overlooked detail can lead to inventory discrepancies, stockouts, or worse—customer dissatisfaction. This guide walks you through the entire process, making sure you’re not just ticking off boxes but actively enhancing your inventory management practices.
Our Goal
The primary aim of this process is to guarantee that all incoming shipments are meticulously inspected and received, ensuring the accuracy of inventory records and preventing any discrepancies. By maintaining the integrity of your stock levels, you’re safeguarding the quality of your inventory, which directly impacts customer satisfaction and your bottom line.
What We're Covering
This guide is designed for the Inventory Management team and warehouse staff responsible for receiving and inspecting shipments. We’ll cover everything from checking the accuracy of incoming goods to documenting their receipt and updating your inventory records. By the end of this process, you’ll have a clear, actionable approach to handling incoming shipments efficiently and effectively.
When to Do This
The steps outlined in this guide should be followed every time a new shipment arrives. This includes an initial inspection upon arrival, followed by thorough documentation and proper storage of the received goods. Consistency in this process is key to maintaining accurate and reliable inventory records.
Why It Matters
The inspection and receipt of incoming shipments are not just administrative tasks; they are critical control points in your inventory management system. By executing this process properly, you:
● Prevent Inventory Discrepancies: Accurate inspections ensure that your records reflect the actual stock on hand, helping avoid stockouts and overstocking.
● Ensure Product Quality: By catching any damages or defects early, you maintain the integrity of the products entering your inventory, reducing the risk of customer complaints.
● Maintain Accurate Records: Proper documentation of received goods ensures that your inventory system is always up-to-date, which is crucial for forecasting and replenishment.
Things You'll Need
To carry out the inspection and receipt of shipments efficiently, you’ll need the following tools and resources:
● Purchase Orders (POs): The blueprint for what you’re expecting to receive.
● Delivery Notes and Invoices: These documents accompany the shipment and should match the details on the PO.
● Barcode Scanners: Essential for updating inventory records quickly and accurately.
● Inspection Checklists: A standardized form to ensure no detail is overlooked during inspection.
● Inventory Management Software: The central hub where all inventory data is updated.
● Storage Solutions: Shelves, bins, or other storage options for organizing the received goods.
● Camera: To document any damages or discrepancies, providing evidence for supplier claims.
Who Does This
While the article omits detailed roles, it’s essential to ensure that the right people are involved in each step of this process. Coordination among your inventory management team, warehouse staff, and any relevant stakeholders is key to a smooth operation.
How to Do It: Step-by-Step / Guidelines
1. Prepare for Shipment Arrival
● Review Purchase Orders (POs): Before the shipment arrives, review the POs to know exactly what to expect—items, quantities, and any specific instructions. This sets the stage for a smooth receiving process.
● Set up the Receiving Area: Clear and organize the receiving area to ensure there’s ample space for the incoming goods. Gather all the necessary tools and equipment for inspection.
2. Inspect Shipment Upon Arrival
● Verify Delivery Documents: Upon arrival, the first step is to compare the delivery note and invoice against the PO. Ensure that the shipment details, including item descriptions and quantities, match your expectations.
● Conduct a Visual Inspection: Before even opening the boxes, check the external packaging for any signs of damage or tampering. This is your first line of defense against potential issues.
● Open and Inspect the Contents: Carefully open the packages and inspect each item. Look for damages, defects, or any discrepancies in the items received. This step is crucial for maintaining the quality of your inventory.
3. Document and Report Findings
● Record Inspection Results: Use the inspection checklist to document the condition and quantities of the received items. This documentation should be detailed and thorough.
● Report Issues to the Supplier: If any damages or discrepancies are found, contact the supplier immediately. Provide photographic evidence and detailed descriptions to expedite the resolution process.
● Arrange for Returns or Replacements: Coordinate with the supplier to handle any returns or replacements. Ensure that all communication and agreements are documented to avoid any misunderstandings.
4. Update Inventory Records
● Enter Received Items into Inventory Management Software: Update your inventory records with the details of the received goods. This ensures that your stock levels are accurate and reflective of the actual inventory.
● Label and Store Received Items: Once the items are verified and documented, label each one with appropriate barcodes or identifiers. Store them in their designated locations within the warehouse to maintain organization and accessibility.
5. Finalize Receipt Process
● File All Documentation: Organize and file all related documents, including POs, delivery notes, and inspection checklists. These records should be easily accessible for future reference or audits.
● Conduct a Post-Receipt Review: Review the entire receipt process to identify any areas for improvement. This ongoing evaluation helps in refining the process for future shipments.
Important Tips
While safety protocols and compliance regulations are crucial, they’ve been omitted in this article to focus on the inspection and receiving process. However, here are some practical tips to enhance the efficiency and accuracy of your operations:
● Create a Standard Operating Procedure (SOP): Standardize the receiving process by creating a detailed SOP that everyone on the team can follow. This reduces variability and increases consistency.
● Use Technology to Your Advantage: Leverage inventory management software, barcode scanners, and mobile devices to streamline the process. Automation can significantly reduce manual errors and save time.
● Continuous Training and Improvement: Regularly train your staff on the latest best practices and technologies in inventory management. Encourage feedback and continuously refine the process for better outcomes.
By following these guidelines, you can ensure that your incoming shipments are inspected and received accurately, maintaining the integrity of your inventory and supporting the overall efficiency of your operations. The proper receipt of shipments is more than just a routine task—it's a critical component of your business’s success
In the fast-paced world of inventory management, ensuring the accuracy and quality of incoming shipments is crucial. Every missed step or overlooked detail can lead to inventory discrepancies, stockouts, or worse—customer dissatisfaction. This guide walks you through the entire process, making sure you’re not just ticking off boxes but actively enhancing your inventory management practices.
Our Goal
The primary aim of this process is to guarantee that all incoming shipments are meticulously inspected and received, ensuring the accuracy of inventory records and preventing any discrepancies. By maintaining the integrity of your stock levels, you’re safeguarding the quality of your inventory, which directly impacts customer satisfaction and your bottom line.
What We're Covering
This guide is designed for the Inventory Management team and warehouse staff responsible for receiving and inspecting shipments. We’ll cover everything from checking the accuracy of incoming goods to documenting their receipt and updating your inventory records. By the end of this process, you’ll have a clear, actionable approach to handling incoming shipments efficiently and effectively.
When to Do This
The steps outlined in this guide should be followed every time a new shipment arrives. This includes an initial inspection upon arrival, followed by thorough documentation and proper storage of the received goods. Consistency in this process is key to maintaining accurate and reliable inventory records.
Why It Matters
The inspection and receipt of incoming shipments are not just administrative tasks; they are critical control points in your inventory management system. By executing this process properly, you:
● Prevent Inventory Discrepancies: Accurate inspections ensure that your records reflect the actual stock on hand, helping avoid stockouts and overstocking.
● Ensure Product Quality: By catching any damages or defects early, you maintain the integrity of the products entering your inventory, reducing the risk of customer complaints.
● Maintain Accurate Records: Proper documentation of received goods ensures that your inventory system is always up-to-date, which is crucial for forecasting and replenishment.
Things You'll Need
To carry out the inspection and receipt of shipments efficiently, you’ll need the following tools and resources:
● Purchase Orders (POs): The blueprint for what you’re expecting to receive.
● Delivery Notes and Invoices: These documents accompany the shipment and should match the details on the PO.
● Barcode Scanners: Essential for updating inventory records quickly and accurately.
● Inspection Checklists: A standardized form to ensure no detail is overlooked during inspection.
● Inventory Management Software: The central hub where all inventory data is updated.
● Storage Solutions: Shelves, bins, or other storage options for organizing the received goods.
● Camera: To document any damages or discrepancies, providing evidence for supplier claims.
Who Does This
While the article omits detailed roles, it’s essential to ensure that the right people are involved in each step of this process. Coordination among your inventory management team, warehouse staff, and any relevant stakeholders is key to a smooth operation.
How to Do It: Step-by-Step / Guidelines
1. Prepare for Shipment Arrival
● Review Purchase Orders (POs): Before the shipment arrives, review the POs to know exactly what to expect—items, quantities, and any specific instructions. This sets the stage for a smooth receiving process.
● Set up the Receiving Area: Clear and organize the receiving area to ensure there’s ample space for the incoming goods. Gather all the necessary tools and equipment for inspection.
2. Inspect Shipment Upon Arrival
● Verify Delivery Documents: Upon arrival, the first step is to compare the delivery note and invoice against the PO. Ensure that the shipment details, including item descriptions and quantities, match your expectations.
● Conduct a Visual Inspection: Before even opening the boxes, check the external packaging for any signs of damage or tampering. This is your first line of defense against potential issues.
● Open and Inspect the Contents: Carefully open the packages and inspect each item. Look for damages, defects, or any discrepancies in the items received. This step is crucial for maintaining the quality of your inventory.
3. Document and Report Findings
● Record Inspection Results: Use the inspection checklist to document the condition and quantities of the received items. This documentation should be detailed and thorough.
● Report Issues to the Supplier: If any damages or discrepancies are found, contact the supplier immediately. Provide photographic evidence and detailed descriptions to expedite the resolution process.
● Arrange for Returns or Replacements: Coordinate with the supplier to handle any returns or replacements. Ensure that all communication and agreements are documented to avoid any misunderstandings.
4. Update Inventory Records
● Enter Received Items into Inventory Management Software: Update your inventory records with the details of the received goods. This ensures that your stock levels are accurate and reflective of the actual inventory.
● Label and Store Received Items: Once the items are verified and documented, label each one with appropriate barcodes or identifiers. Store them in their designated locations within the warehouse to maintain organization and accessibility.
5. Finalize Receipt Process
● File All Documentation: Organize and file all related documents, including POs, delivery notes, and inspection checklists. These records should be easily accessible for future reference or audits.
● Conduct a Post-Receipt Review: Review the entire receipt process to identify any areas for improvement. This ongoing evaluation helps in refining the process for future shipments.
Important Tips
While safety protocols and compliance regulations are crucial, they’ve been omitted in this article to focus on the inspection and receiving process. However, here are some practical tips to enhance the efficiency and accuracy of your operations:
● Create a Standard Operating Procedure (SOP): Standardize the receiving process by creating a detailed SOP that everyone on the team can follow. This reduces variability and increases consistency.
● Use Technology to Your Advantage: Leverage inventory management software, barcode scanners, and mobile devices to streamline the process. Automation can significantly reduce manual errors and save time.
● Continuous Training and Improvement: Regularly train your staff on the latest best practices and technologies in inventory management. Encourage feedback and continuously refine the process for better outcomes.
By following these guidelines, you can ensure that your incoming shipments are inspected and received accurately, maintaining the integrity of your inventory and supporting the overall efficiency of your operations. The proper receipt of shipments is more than just a routine task—it's a critical component of your business’s success
In the fast-paced world of inventory management, ensuring the accuracy and quality of incoming shipments is crucial. Every missed step or overlooked detail can lead to inventory discrepancies, stockouts, or worse—customer dissatisfaction. This guide walks you through the entire process, making sure you’re not just ticking off boxes but actively enhancing your inventory management practices.
Our Goal
The primary aim of this process is to guarantee that all incoming shipments are meticulously inspected and received, ensuring the accuracy of inventory records and preventing any discrepancies. By maintaining the integrity of your stock levels, you’re safeguarding the quality of your inventory, which directly impacts customer satisfaction and your bottom line.
What We're Covering
This guide is designed for the Inventory Management team and warehouse staff responsible for receiving and inspecting shipments. We’ll cover everything from checking the accuracy of incoming goods to documenting their receipt and updating your inventory records. By the end of this process, you’ll have a clear, actionable approach to handling incoming shipments efficiently and effectively.
When to Do This
The steps outlined in this guide should be followed every time a new shipment arrives. This includes an initial inspection upon arrival, followed by thorough documentation and proper storage of the received goods. Consistency in this process is key to maintaining accurate and reliable inventory records.
Why It Matters
The inspection and receipt of incoming shipments are not just administrative tasks; they are critical control points in your inventory management system. By executing this process properly, you:
● Prevent Inventory Discrepancies: Accurate inspections ensure that your records reflect the actual stock on hand, helping avoid stockouts and overstocking.
● Ensure Product Quality: By catching any damages or defects early, you maintain the integrity of the products entering your inventory, reducing the risk of customer complaints.
● Maintain Accurate Records: Proper documentation of received goods ensures that your inventory system is always up-to-date, which is crucial for forecasting and replenishment.
Things You'll Need
To carry out the inspection and receipt of shipments efficiently, you’ll need the following tools and resources:
● Purchase Orders (POs): The blueprint for what you’re expecting to receive.
● Delivery Notes and Invoices: These documents accompany the shipment and should match the details on the PO.
● Barcode Scanners: Essential for updating inventory records quickly and accurately.
● Inspection Checklists: A standardized form to ensure no detail is overlooked during inspection.
● Inventory Management Software: The central hub where all inventory data is updated.
● Storage Solutions: Shelves, bins, or other storage options for organizing the received goods.
● Camera: To document any damages or discrepancies, providing evidence for supplier claims.
Who Does This
While the article omits detailed roles, it’s essential to ensure that the right people are involved in each step of this process. Coordination among your inventory management team, warehouse staff, and any relevant stakeholders is key to a smooth operation.
How to Do It: Step-by-Step / Guidelines
1. Prepare for Shipment Arrival
● Review Purchase Orders (POs): Before the shipment arrives, review the POs to know exactly what to expect—items, quantities, and any specific instructions. This sets the stage for a smooth receiving process.
● Set up the Receiving Area: Clear and organize the receiving area to ensure there’s ample space for the incoming goods. Gather all the necessary tools and equipment for inspection.
2. Inspect Shipment Upon Arrival
● Verify Delivery Documents: Upon arrival, the first step is to compare the delivery note and invoice against the PO. Ensure that the shipment details, including item descriptions and quantities, match your expectations.
● Conduct a Visual Inspection: Before even opening the boxes, check the external packaging for any signs of damage or tampering. This is your first line of defense against potential issues.
● Open and Inspect the Contents: Carefully open the packages and inspect each item. Look for damages, defects, or any discrepancies in the items received. This step is crucial for maintaining the quality of your inventory.
3. Document and Report Findings
● Record Inspection Results: Use the inspection checklist to document the condition and quantities of the received items. This documentation should be detailed and thorough.
● Report Issues to the Supplier: If any damages or discrepancies are found, contact the supplier immediately. Provide photographic evidence and detailed descriptions to expedite the resolution process.
● Arrange for Returns or Replacements: Coordinate with the supplier to handle any returns or replacements. Ensure that all communication and agreements are documented to avoid any misunderstandings.
4. Update Inventory Records
● Enter Received Items into Inventory Management Software: Update your inventory records with the details of the received goods. This ensures that your stock levels are accurate and reflective of the actual inventory.
● Label and Store Received Items: Once the items are verified and documented, label each one with appropriate barcodes or identifiers. Store them in their designated locations within the warehouse to maintain organization and accessibility.
5. Finalize Receipt Process
● File All Documentation: Organize and file all related documents, including POs, delivery notes, and inspection checklists. These records should be easily accessible for future reference or audits.
● Conduct a Post-Receipt Review: Review the entire receipt process to identify any areas for improvement. This ongoing evaluation helps in refining the process for future shipments.
Important Tips
While safety protocols and compliance regulations are crucial, they’ve been omitted in this article to focus on the inspection and receiving process. However, here are some practical tips to enhance the efficiency and accuracy of your operations:
● Create a Standard Operating Procedure (SOP): Standardize the receiving process by creating a detailed SOP that everyone on the team can follow. This reduces variability and increases consistency.
● Use Technology to Your Advantage: Leverage inventory management software, barcode scanners, and mobile devices to streamline the process. Automation can significantly reduce manual errors and save time.
● Continuous Training and Improvement: Regularly train your staff on the latest best practices and technologies in inventory management. Encourage feedback and continuously refine the process for better outcomes.
By following these guidelines, you can ensure that your incoming shipments are inspected and received accurately, maintaining the integrity of your inventory and supporting the overall efficiency of your operations. The proper receipt of shipments is more than just a routine task—it's a critical component of your business’s success