
Contact us
Management and Operations
Embracing Continuous Improvement Leading to Business Excellence
Feb 3, 2025
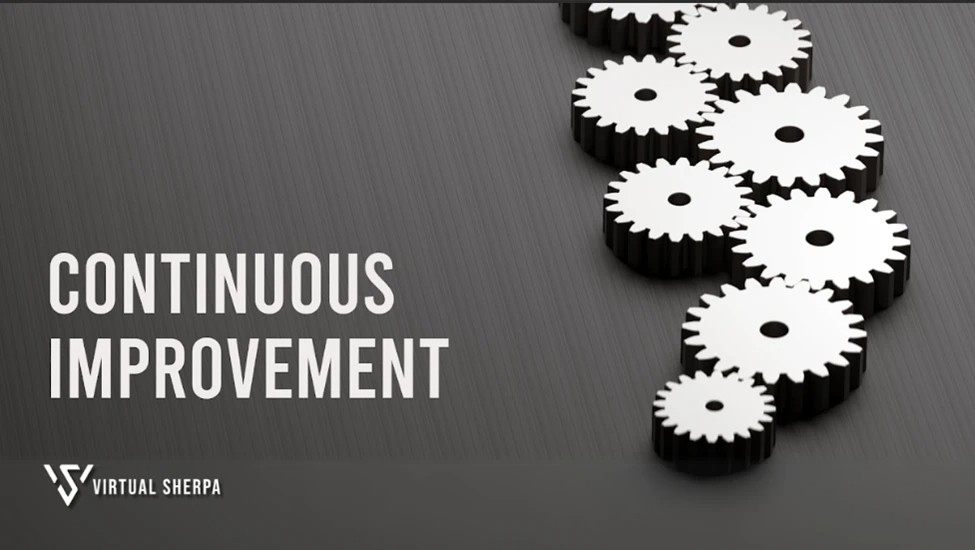
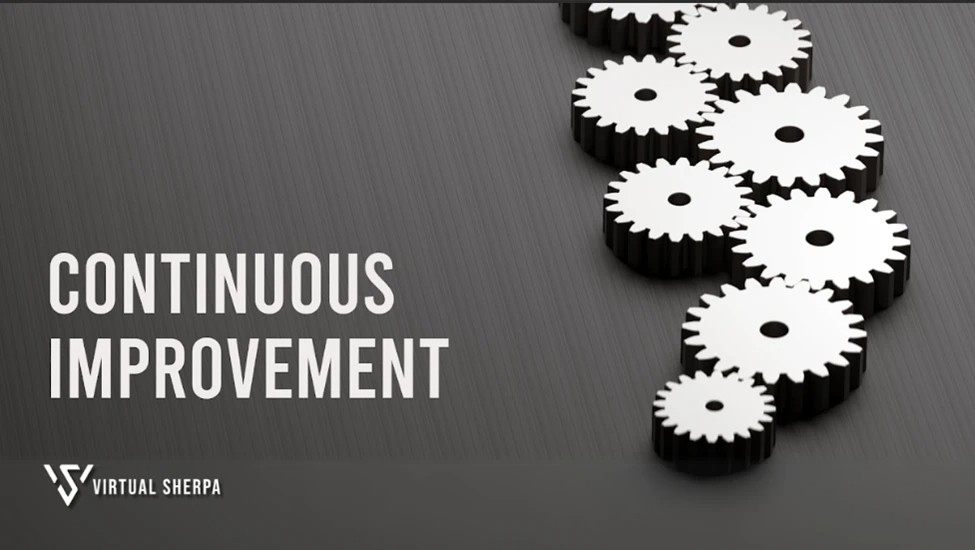
The world is constantly evolving, and businesses must adapt and innovate to stay competitive. Continuous improvement is a vital strategy that focuses on enhancing processes, products, and services to achieve greater efficiency, quality, and customer satisfaction. It’s about making incremental changes that lead to significant, long-term benefits for your organization.
This guide will explore the essentials of continuous improvement, including its importance, core principles, methodologies, and practical strategies for implementation.
What is Continuous Improvement?
Continuous improvement is an ongoing effort to enhance products, services, or processes through incremental and breakthrough improvements. It’s about constantly seeking ways to improve efficiency, reduce waste, increase quality, and deliver better value to customers. Rather than resting on past successes, organizations that embrace continuous improvement are always looking for ways to get better, faster, and more innovative.
Why Continuous Improvement Matters
Enhances Efficiency: Continuous improvement helps identify inefficiencies and waste in processes, enabling organizations to simplify and organize operations and reduce costs. This leads to improved productivity and profitability.
Improves Quality: By focusing on incremental improvements, organizations can enhance the quality of their products and services, leading to higher customer satisfaction and loyalty.
Promotes Innovation: A culture of continuous improvement encourages creativity and innovation, as employees are empowered to suggest new ideas and approaches. This can lead to breakthrough innovations that drive competitive advantage.
Builds Resilience: Organizations that embrace continuous improvement are better equipped to adapt to changes in the market or industry. This resilience enables them to thrive in an ever-changing business environment.
Engages Employees: Continuous improvement fosters a sense of ownership and engagement among employees, as they are actively involved in the process of making improvements. This can lead to higher morale, job satisfaction, and retention.
Core Principles of Continuous Improvement
To implement a successful continuous improvement program, it’s essential to understand its core principles:
Focus on the Customer: Continuous improvement is ultimately about delivering better value to customers. This means understanding customer needs and expectations and continuously finding ways to meet or exceed them.
Involve Everyone: Continuous improvement is not just the responsibility of management or a specific department; it’s a company-wide effort. Involve employees at all levels and encourage them to contribute ideas and suggestions for improvement.
Embrace Change: Continuous improvement requires a willingness to change and adapt. This means being open to new ideas, experimenting with different approaches, and learning from failures.
Measure and Analyze: To identify areas for improvement, it’s essential to measure and analyze performance. This involves collecting data, tracking key performance indicators (KPIs), and using analytical tools to identify trends and areas for improvement.
Make Incremental Improvements: Continuous improvement is about making small, incremental changes that add up to significant improvements over time. This approach reduces risk and makes it easier to implement and sustain changes.
Key Methodologies for Continuous Improvement
There are several methodologies and frameworks that organizations can use to implement continuous improvement. Here are some of the most popular ones:
Kaizen: Kaizen is a Japanese philosophy that focuses on continuous, incremental improvements. It involves all employees, from management to frontline workers, in identifying areas for improvement and implementing changes. Kaizen emphasizes a culture of continuous learning and collaboration.
Lean: Lean is a methodology that focuses on maximizing value for customers by eliminating waste and improving efficiency. It involves identifying value-added and non-value-added activities in a process and finding ways to eliminate or reduce the latter. Lean principles can be applied to any industry or process to enhance efficiency and reduce costs.
Six Sigma: Six Sigma is a data-driven methodology that aims to improve quality by identifying and eliminating defects in processes. It involves using statistical tools and techniques to measure performance, analyze data, and implement improvements. Six Sigma is often used in manufacturing and other industries where quality and consistency are critical.
PDCA (Plan-Do-Check-Act): The PDCA cycle, also known as the Deming Cycle, is a simple but effective framework for continuous improvement. It involves four steps: Plan (identify an opportunity for improvement and develop a plan), Do (implement the plan), Check (evaluate the results), and Act (make adjustments based on the findings).
Agile: Originally developed for software development, Agile is a methodology that emphasizes flexibility, collaboration, and rapid iteration. Agile involves breaking work into small, manageable tasks and continuously testing and refining them based on feedback. This approach allows for quick adjustments and continuous improvement.
Steps to Implement Continuous Improvement in Your Organization
Step 1: Establish a Continuous Improvement Culture
The foundation of a successful continuous improvement program is a strong organizational culture that supports and encourages improvement. This involves:
● Leadership Commitment: Leaders must demonstrate a commitment to continuous improvement by setting an example, providing resources, and recognizing and rewarding employees for their efforts. This helps to create a culture where continuous improvement is valued and encouraged.
● Employee Involvement: Encourage all employees to participate in continuous improvement efforts by providing training, resources, and opportunities to contribute ideas. Create a safe environment where employees feel comfortable sharing suggestions and experimenting with new approaches.
Step 2: Identify Improvement Opportunities
Once a culture of continuous improvement is established, the next step is to identify opportunities for improvement. This involves:
● Data Collection: Collect data on key performance indicators (KPIs), customer feedback, and other relevant metrics to identify areas where improvements can be made. Use tools such as surveys, focus groups, and performance dashboards to gather data.
● Process Mapping: Map out your organization's processes to identify inefficiencies,obstructions, and areas of waste. This provides a visual representation of how work is done and helps identify areas for improvement.
Step 3: Develop Improvement Plans
After identifying improvement opportunities, the next step is to develop improvement plans that outline specific actions and resources needed to achieve the desired results. This involves:
● Setting Goals: Set clear, measurable goals for each improvement initiative. These goals should align with the organization’s strategic objectives and provide a clear direction for the improvement effort.
● Identifying Actions: Identify specific actions that need to be taken to achieve the improvement goals. This could include changes to processes, training programs, or new technologies.
Step 4: Implement and Test Improvements
Once improvement plans have been developed, the next step is to implement and test the changes. This involves:
● Pilot Testing: Start with a small-scale pilot test to evaluate the effectiveness of the improvement before rolling it out across the organization. This allows you to identify any issues or challenges and make adjustments before full implementation.
● Monitoring Progress: Monitor the progress of the improvement initiative by tracking KPIs and collecting feedback from employees and customers. This helps ensure that the improvement is on track and achieving the desired results.
Step 5: Review and Refine
Continuous improvement is an ongoing process that requires regular review and refinement. This involves:
● Evaluating Results: Evaluate the results of the improvement initiative to determine its effectiveness. Use data and feedback to assess whether the improvement has achieved its goals and identify any areas for further improvement.
● Making Adjustments: Based on the evaluation, make any necessary adjustments to the improvement initiative. This could involve refining processes, providing additional training, or making changes to the improvement plan.
Best Practices for Continuous Improvement
To maximize the effectiveness of your continuous improvement efforts, follow these best practices:
Encourage Experimentation: Continuous improvement involves trying new approaches and learning from failures. Encourage a culture of experimentation where employees feel comfortable taking risks and trying new ideas.
Technology: Use technology to support continuous improvement efforts, such as data analytics tools, process automation software, and collaboration platforms. These tools can help streamline processes, improve data accuracy, and facilitate communication.
Celebrate Successes: Recognize and celebrate successes, no matter how small. Celebrating achievements helps to reinforce a culture of continuous improvement and motivates employees to continue contributing.
Focus on the Customer: Always keep the customer in mind when making improvements. Focus on delivering better value, enhancing the customer experience, and meeting or exceeding customer expectations.
Keep It Simple: Continuous improvement doesn’t have to be complicated. Focus on making small, incremental changes that are easy to implement and sustain. This approach reduces risk and makes it easier to maintain momentum.
Conclusion
Continuous improvement is a powerful strategy that can drive innovation, enhance performance, and contribute to long-term success. By embracing a culture of continuous improvement and following the steps outlined in this guide, you can create an environment where employees are empowered to make positive changes, processes are optimized, and customers receive exceptional value.
Remember, continuous improvement is not a one-time initiative but an ongoing journey that requires commitment, collaboration, and a willingness to adapt. By investing in continuous improvement, you are setting your organization up for a future of growth, innovation, and excellence.
The world is constantly evolving, and businesses must adapt and innovate to stay competitive. Continuous improvement is a vital strategy that focuses on enhancing processes, products, and services to achieve greater efficiency, quality, and customer satisfaction. It’s about making incremental changes that lead to significant, long-term benefits for your organization.
This guide will explore the essentials of continuous improvement, including its importance, core principles, methodologies, and practical strategies for implementation.
What is Continuous Improvement?
Continuous improvement is an ongoing effort to enhance products, services, or processes through incremental and breakthrough improvements. It’s about constantly seeking ways to improve efficiency, reduce waste, increase quality, and deliver better value to customers. Rather than resting on past successes, organizations that embrace continuous improvement are always looking for ways to get better, faster, and more innovative.
Why Continuous Improvement Matters
Enhances Efficiency: Continuous improvement helps identify inefficiencies and waste in processes, enabling organizations to simplify and organize operations and reduce costs. This leads to improved productivity and profitability.
Improves Quality: By focusing on incremental improvements, organizations can enhance the quality of their products and services, leading to higher customer satisfaction and loyalty.
Promotes Innovation: A culture of continuous improvement encourages creativity and innovation, as employees are empowered to suggest new ideas and approaches. This can lead to breakthrough innovations that drive competitive advantage.
Builds Resilience: Organizations that embrace continuous improvement are better equipped to adapt to changes in the market or industry. This resilience enables them to thrive in an ever-changing business environment.
Engages Employees: Continuous improvement fosters a sense of ownership and engagement among employees, as they are actively involved in the process of making improvements. This can lead to higher morale, job satisfaction, and retention.
Core Principles of Continuous Improvement
To implement a successful continuous improvement program, it’s essential to understand its core principles:
Focus on the Customer: Continuous improvement is ultimately about delivering better value to customers. This means understanding customer needs and expectations and continuously finding ways to meet or exceed them.
Involve Everyone: Continuous improvement is not just the responsibility of management or a specific department; it’s a company-wide effort. Involve employees at all levels and encourage them to contribute ideas and suggestions for improvement.
Embrace Change: Continuous improvement requires a willingness to change and adapt. This means being open to new ideas, experimenting with different approaches, and learning from failures.
Measure and Analyze: To identify areas for improvement, it’s essential to measure and analyze performance. This involves collecting data, tracking key performance indicators (KPIs), and using analytical tools to identify trends and areas for improvement.
Make Incremental Improvements: Continuous improvement is about making small, incremental changes that add up to significant improvements over time. This approach reduces risk and makes it easier to implement and sustain changes.
Key Methodologies for Continuous Improvement
There are several methodologies and frameworks that organizations can use to implement continuous improvement. Here are some of the most popular ones:
Kaizen: Kaizen is a Japanese philosophy that focuses on continuous, incremental improvements. It involves all employees, from management to frontline workers, in identifying areas for improvement and implementing changes. Kaizen emphasizes a culture of continuous learning and collaboration.
Lean: Lean is a methodology that focuses on maximizing value for customers by eliminating waste and improving efficiency. It involves identifying value-added and non-value-added activities in a process and finding ways to eliminate or reduce the latter. Lean principles can be applied to any industry or process to enhance efficiency and reduce costs.
Six Sigma: Six Sigma is a data-driven methodology that aims to improve quality by identifying and eliminating defects in processes. It involves using statistical tools and techniques to measure performance, analyze data, and implement improvements. Six Sigma is often used in manufacturing and other industries where quality and consistency are critical.
PDCA (Plan-Do-Check-Act): The PDCA cycle, also known as the Deming Cycle, is a simple but effective framework for continuous improvement. It involves four steps: Plan (identify an opportunity for improvement and develop a plan), Do (implement the plan), Check (evaluate the results), and Act (make adjustments based on the findings).
Agile: Originally developed for software development, Agile is a methodology that emphasizes flexibility, collaboration, and rapid iteration. Agile involves breaking work into small, manageable tasks and continuously testing and refining them based on feedback. This approach allows for quick adjustments and continuous improvement.
Steps to Implement Continuous Improvement in Your Organization
Step 1: Establish a Continuous Improvement Culture
The foundation of a successful continuous improvement program is a strong organizational culture that supports and encourages improvement. This involves:
● Leadership Commitment: Leaders must demonstrate a commitment to continuous improvement by setting an example, providing resources, and recognizing and rewarding employees for their efforts. This helps to create a culture where continuous improvement is valued and encouraged.
● Employee Involvement: Encourage all employees to participate in continuous improvement efforts by providing training, resources, and opportunities to contribute ideas. Create a safe environment where employees feel comfortable sharing suggestions and experimenting with new approaches.
Step 2: Identify Improvement Opportunities
Once a culture of continuous improvement is established, the next step is to identify opportunities for improvement. This involves:
● Data Collection: Collect data on key performance indicators (KPIs), customer feedback, and other relevant metrics to identify areas where improvements can be made. Use tools such as surveys, focus groups, and performance dashboards to gather data.
● Process Mapping: Map out your organization's processes to identify inefficiencies,obstructions, and areas of waste. This provides a visual representation of how work is done and helps identify areas for improvement.
Step 3: Develop Improvement Plans
After identifying improvement opportunities, the next step is to develop improvement plans that outline specific actions and resources needed to achieve the desired results. This involves:
● Setting Goals: Set clear, measurable goals for each improvement initiative. These goals should align with the organization’s strategic objectives and provide a clear direction for the improvement effort.
● Identifying Actions: Identify specific actions that need to be taken to achieve the improvement goals. This could include changes to processes, training programs, or new technologies.
Step 4: Implement and Test Improvements
Once improvement plans have been developed, the next step is to implement and test the changes. This involves:
● Pilot Testing: Start with a small-scale pilot test to evaluate the effectiveness of the improvement before rolling it out across the organization. This allows you to identify any issues or challenges and make adjustments before full implementation.
● Monitoring Progress: Monitor the progress of the improvement initiative by tracking KPIs and collecting feedback from employees and customers. This helps ensure that the improvement is on track and achieving the desired results.
Step 5: Review and Refine
Continuous improvement is an ongoing process that requires regular review and refinement. This involves:
● Evaluating Results: Evaluate the results of the improvement initiative to determine its effectiveness. Use data and feedback to assess whether the improvement has achieved its goals and identify any areas for further improvement.
● Making Adjustments: Based on the evaluation, make any necessary adjustments to the improvement initiative. This could involve refining processes, providing additional training, or making changes to the improvement plan.
Best Practices for Continuous Improvement
To maximize the effectiveness of your continuous improvement efforts, follow these best practices:
Encourage Experimentation: Continuous improvement involves trying new approaches and learning from failures. Encourage a culture of experimentation where employees feel comfortable taking risks and trying new ideas.
Technology: Use technology to support continuous improvement efforts, such as data analytics tools, process automation software, and collaboration platforms. These tools can help streamline processes, improve data accuracy, and facilitate communication.
Celebrate Successes: Recognize and celebrate successes, no matter how small. Celebrating achievements helps to reinforce a culture of continuous improvement and motivates employees to continue contributing.
Focus on the Customer: Always keep the customer in mind when making improvements. Focus on delivering better value, enhancing the customer experience, and meeting or exceeding customer expectations.
Keep It Simple: Continuous improvement doesn’t have to be complicated. Focus on making small, incremental changes that are easy to implement and sustain. This approach reduces risk and makes it easier to maintain momentum.
Conclusion
Continuous improvement is a powerful strategy that can drive innovation, enhance performance, and contribute to long-term success. By embracing a culture of continuous improvement and following the steps outlined in this guide, you can create an environment where employees are empowered to make positive changes, processes are optimized, and customers receive exceptional value.
Remember, continuous improvement is not a one-time initiative but an ongoing journey that requires commitment, collaboration, and a willingness to adapt. By investing in continuous improvement, you are setting your organization up for a future of growth, innovation, and excellence.
The world is constantly evolving, and businesses must adapt and innovate to stay competitive. Continuous improvement is a vital strategy that focuses on enhancing processes, products, and services to achieve greater efficiency, quality, and customer satisfaction. It’s about making incremental changes that lead to significant, long-term benefits for your organization.
This guide will explore the essentials of continuous improvement, including its importance, core principles, methodologies, and practical strategies for implementation.
What is Continuous Improvement?
Continuous improvement is an ongoing effort to enhance products, services, or processes through incremental and breakthrough improvements. It’s about constantly seeking ways to improve efficiency, reduce waste, increase quality, and deliver better value to customers. Rather than resting on past successes, organizations that embrace continuous improvement are always looking for ways to get better, faster, and more innovative.
Why Continuous Improvement Matters
Enhances Efficiency: Continuous improvement helps identify inefficiencies and waste in processes, enabling organizations to simplify and organize operations and reduce costs. This leads to improved productivity and profitability.
Improves Quality: By focusing on incremental improvements, organizations can enhance the quality of their products and services, leading to higher customer satisfaction and loyalty.
Promotes Innovation: A culture of continuous improvement encourages creativity and innovation, as employees are empowered to suggest new ideas and approaches. This can lead to breakthrough innovations that drive competitive advantage.
Builds Resilience: Organizations that embrace continuous improvement are better equipped to adapt to changes in the market or industry. This resilience enables them to thrive in an ever-changing business environment.
Engages Employees: Continuous improvement fosters a sense of ownership and engagement among employees, as they are actively involved in the process of making improvements. This can lead to higher morale, job satisfaction, and retention.
Core Principles of Continuous Improvement
To implement a successful continuous improvement program, it’s essential to understand its core principles:
Focus on the Customer: Continuous improvement is ultimately about delivering better value to customers. This means understanding customer needs and expectations and continuously finding ways to meet or exceed them.
Involve Everyone: Continuous improvement is not just the responsibility of management or a specific department; it’s a company-wide effort. Involve employees at all levels and encourage them to contribute ideas and suggestions for improvement.
Embrace Change: Continuous improvement requires a willingness to change and adapt. This means being open to new ideas, experimenting with different approaches, and learning from failures.
Measure and Analyze: To identify areas for improvement, it’s essential to measure and analyze performance. This involves collecting data, tracking key performance indicators (KPIs), and using analytical tools to identify trends and areas for improvement.
Make Incremental Improvements: Continuous improvement is about making small, incremental changes that add up to significant improvements over time. This approach reduces risk and makes it easier to implement and sustain changes.
Key Methodologies for Continuous Improvement
There are several methodologies and frameworks that organizations can use to implement continuous improvement. Here are some of the most popular ones:
Kaizen: Kaizen is a Japanese philosophy that focuses on continuous, incremental improvements. It involves all employees, from management to frontline workers, in identifying areas for improvement and implementing changes. Kaizen emphasizes a culture of continuous learning and collaboration.
Lean: Lean is a methodology that focuses on maximizing value for customers by eliminating waste and improving efficiency. It involves identifying value-added and non-value-added activities in a process and finding ways to eliminate or reduce the latter. Lean principles can be applied to any industry or process to enhance efficiency and reduce costs.
Six Sigma: Six Sigma is a data-driven methodology that aims to improve quality by identifying and eliminating defects in processes. It involves using statistical tools and techniques to measure performance, analyze data, and implement improvements. Six Sigma is often used in manufacturing and other industries where quality and consistency are critical.
PDCA (Plan-Do-Check-Act): The PDCA cycle, also known as the Deming Cycle, is a simple but effective framework for continuous improvement. It involves four steps: Plan (identify an opportunity for improvement and develop a plan), Do (implement the plan), Check (evaluate the results), and Act (make adjustments based on the findings).
Agile: Originally developed for software development, Agile is a methodology that emphasizes flexibility, collaboration, and rapid iteration. Agile involves breaking work into small, manageable tasks and continuously testing and refining them based on feedback. This approach allows for quick adjustments and continuous improvement.
Steps to Implement Continuous Improvement in Your Organization
Step 1: Establish a Continuous Improvement Culture
The foundation of a successful continuous improvement program is a strong organizational culture that supports and encourages improvement. This involves:
● Leadership Commitment: Leaders must demonstrate a commitment to continuous improvement by setting an example, providing resources, and recognizing and rewarding employees for their efforts. This helps to create a culture where continuous improvement is valued and encouraged.
● Employee Involvement: Encourage all employees to participate in continuous improvement efforts by providing training, resources, and opportunities to contribute ideas. Create a safe environment where employees feel comfortable sharing suggestions and experimenting with new approaches.
Step 2: Identify Improvement Opportunities
Once a culture of continuous improvement is established, the next step is to identify opportunities for improvement. This involves:
● Data Collection: Collect data on key performance indicators (KPIs), customer feedback, and other relevant metrics to identify areas where improvements can be made. Use tools such as surveys, focus groups, and performance dashboards to gather data.
● Process Mapping: Map out your organization's processes to identify inefficiencies,obstructions, and areas of waste. This provides a visual representation of how work is done and helps identify areas for improvement.
Step 3: Develop Improvement Plans
After identifying improvement opportunities, the next step is to develop improvement plans that outline specific actions and resources needed to achieve the desired results. This involves:
● Setting Goals: Set clear, measurable goals for each improvement initiative. These goals should align with the organization’s strategic objectives and provide a clear direction for the improvement effort.
● Identifying Actions: Identify specific actions that need to be taken to achieve the improvement goals. This could include changes to processes, training programs, or new technologies.
Step 4: Implement and Test Improvements
Once improvement plans have been developed, the next step is to implement and test the changes. This involves:
● Pilot Testing: Start with a small-scale pilot test to evaluate the effectiveness of the improvement before rolling it out across the organization. This allows you to identify any issues or challenges and make adjustments before full implementation.
● Monitoring Progress: Monitor the progress of the improvement initiative by tracking KPIs and collecting feedback from employees and customers. This helps ensure that the improvement is on track and achieving the desired results.
Step 5: Review and Refine
Continuous improvement is an ongoing process that requires regular review and refinement. This involves:
● Evaluating Results: Evaluate the results of the improvement initiative to determine its effectiveness. Use data and feedback to assess whether the improvement has achieved its goals and identify any areas for further improvement.
● Making Adjustments: Based on the evaluation, make any necessary adjustments to the improvement initiative. This could involve refining processes, providing additional training, or making changes to the improvement plan.
Best Practices for Continuous Improvement
To maximize the effectiveness of your continuous improvement efforts, follow these best practices:
Encourage Experimentation: Continuous improvement involves trying new approaches and learning from failures. Encourage a culture of experimentation where employees feel comfortable taking risks and trying new ideas.
Technology: Use technology to support continuous improvement efforts, such as data analytics tools, process automation software, and collaboration platforms. These tools can help streamline processes, improve data accuracy, and facilitate communication.
Celebrate Successes: Recognize and celebrate successes, no matter how small. Celebrating achievements helps to reinforce a culture of continuous improvement and motivates employees to continue contributing.
Focus on the Customer: Always keep the customer in mind when making improvements. Focus on delivering better value, enhancing the customer experience, and meeting or exceeding customer expectations.
Keep It Simple: Continuous improvement doesn’t have to be complicated. Focus on making small, incremental changes that are easy to implement and sustain. This approach reduces risk and makes it easier to maintain momentum.
Conclusion
Continuous improvement is a powerful strategy that can drive innovation, enhance performance, and contribute to long-term success. By embracing a culture of continuous improvement and following the steps outlined in this guide, you can create an environment where employees are empowered to make positive changes, processes are optimized, and customers receive exceptional value.
Remember, continuous improvement is not a one-time initiative but an ongoing journey that requires commitment, collaboration, and a willingness to adapt. By investing in continuous improvement, you are setting your organization up for a future of growth, innovation, and excellence.